HOME IMPROVEMENT
Essential Insights into Conveyor Impact Rollers: Design, Applications, and Maintenance
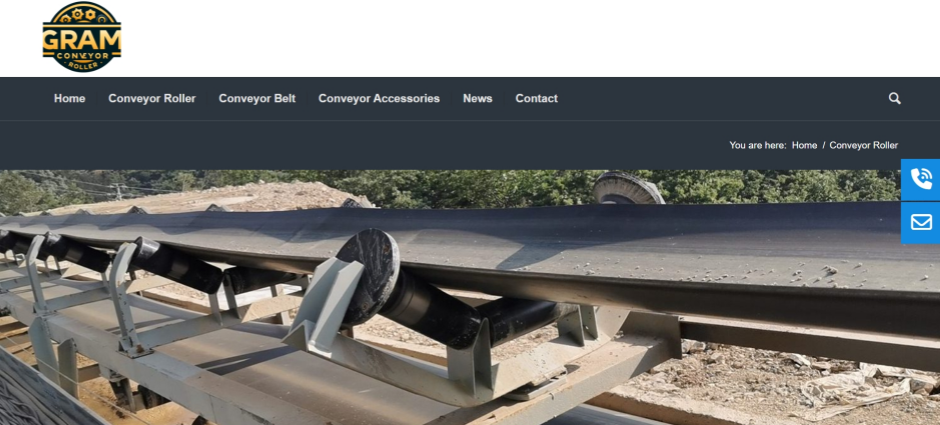
Conveyor impact rollers are essential components in material handling systems, designed to absorb and reduce the impact of heavy loads and sharp-edged materials on conveyor belts. They play a crucial role in protecting both the conveyor system and the transported goods, ensuring smooth and efficient operations. Conveyor rollers, in general, are vital for the efficient movement of goods, and among them, nylon conveyor rollers have gained prominence due to their exceptional properties. Known for their durability, lightweight nature, and resistance to corrosion, nylon rollers offer significant advantages over traditional materials. Their low friction and noise reduction capabilities make them ideal for various industrial applications, from manufacturing to logistics. This article delves into the benefits, applications, and future trends of nylon conveyor rollers in modern industry.
Key Features of Conveyor Impact Rollers
Design and Construction
Conveyor impact rollers are meticulously designed to endure the harshest conditions in material handling environments. Typically constructed with a robust steel shell, these rollers are built to provide a sturdy framework that can withstand heavy impacts. The core of the roller often includes shock-absorbing materials such as rubber rings or discs, strategically placed to cushion the impact and reduce wear on the conveyor belt. The design also incorporates high-quality bearings that ensure smooth rotation and longevity. Additionally, the outer surfac
e of impact rollers is treated or coated to resist abrasion and corrosion, enhancing their durability and operational efficiency.
Impact Absorption Capabilities
The primary function of impact rollers is to absorb and dissipate the energy from heavy or sharp-edged loads, preventing damage to the conveyor belt and extending its service life. The shock-absorbing elements within the rollers, such as rubber rings, are crucial for this purpose. These elements compress under the weight of the load, effectively cushioning the impact and reducing the stress on the entire conveyor system. This absorption capability not only protects the belt but also minimizes the risk of material spillage and damage t
o the transported goods, ensuring a smooth and reliable operation.
Common Sizes and Dimensions
Conveyor impact rollers come in various sizes and dimensions to accommodate different conveyor systems and applications. Common diameters range from 89 mm to 159 mm, with lengths varying to suit specific conveyor widths. The shaft diameter and bearing size are also critical specifications, typically standardized to fit seamlessly into existing conveyor frameworks. Custom sizes are often available to meet unique operational requirements, ensuring that the rollers can handle specific load capacities and impact conditions effective
ly.
Role of Nylon in Impact Rollers
Nylon plays a significant role in enhancing the performance of conveyor impact rollers. As a material, nylon offers several beneficial properties, including high tensile strength, excellent wear resistance, and low friction. These characteristics make nylon an ideal choice for the shock-absorbing components within impact rollers. Nylon’s flexibility and resilience allow it to absorb shocks efficiently, reducing the wear and tear on both the rollers and the conveyor belt. Additionally, nylon’s resistance to moisture and chemicals ensures longevity and reliability in diverse industrial environments. The lightweight nature of nylon also contributes to easier handling and installation, further enhancing its suitability for impact roller applications.
By incorporating these key features
, conveyor impact rollers ensure robust performance, protecting conveyor systems and optimizing material handling processes across various industries.
Applications of Conveyor Impact Rollers
Mining
In the mining industry, conveyor impact rollers are indispensable for handling the heavy loads and harsh conditions typical of mining operations. These rollers are used to transport large quantities of ore, rocks, and other raw materials. The robust design and impact absorption capabilities of these rollers protect the conveyor belts from the significant wear and tear caused by the heavy, abrasive materials. The integration of nylon conveyor rollers in mining operations further enhances durability and efficiency. Nylon’s resistance to moisture and chem
icals ensures that the rollers can withstand the demanding environment of mines, reducing maintenance needs and extending the lifespan of the conveyor systems.
Construction
Conveyor impact rollers are also widely used in the construction industry to move building materials such as sand, gravel, and concr
ete. These rollers help in managing the high impact loads generated when heavy construction materials are dropped onto the conveyor belts. The shock-absorbing properties of impact rollers prevent damage to the conveyor system, ensuring continuous and efficient operation. Nylon conveyor rollers are particularly beneficial in construction applications due to their lightweight nature and ease of installation. They provide excellent impact resistance and help reduce operational noise, making construction sites more efficient and safer.
Heavy Manufacturing
In heavy manufacturing industries, conveyor impact rollers play a crucial role in the transportation of large, heavy parts and assemblies. These rollers are designed to handle the substantial impacts and stresses associated with the movement of heavy machinery components and industrial products. The durability and impact absorption capabilities of these rollers are essential for maintaining the integrity of the conveyor systems and ensuring the smooth flow of materials through the manufacturing process. Nylon conveyor rollers are integrated into heavy manufacturing applications to enhance performance. The high tensile strength and wear resistance of nylon make it ideal for managing the rigorous demands of heavy manufacturing, reducing downtime and maintenance costs.
Integration of Nylon Conveyor Rollers in These Applications
The integration of nylon conveyor rollers across various applications in mining, construction, and heavy manufacturing brings numerous benefits:
- Durability and Longevity: Nylon rollers provide superior durability, reducing the frequency of replacements and extending the service life of conveyor systems. This is particularly beneficial in harsh environments like mines and construction sites.
- Reduced Maintenance: The wear resistance and low friction properties of nylon minimize maintenance requirements, saving time and costs associated with frequent repairs and replacements.
- Noise Reduction: Nylon rollers operate more quietly than traditional metal rollers, which is advantageous in noise-sensitive environments such as construction sites and manufacturing plants.
- Lightweight and Easy Installation: The lightweight nature of nylon makes the rollers easier to handle and install, improving operational efficiency and reducing labor costs.
- Resistance to Environmental Factors: Nylon’s resistance to moisture, chemicals, and abrasion ensures reliable performance in diverse industrial settings, from wet and corrosive mining environments to dusty construction sites.
By leveraging the unique properties of nylon, conveyor impact rollers enhance the efficiency, durability, and overall performance of material handling systems in these critical industries.
Sizing and Selection of Conveyor Impact Rollers
Importance of Correct Sizing
Selecting the correct size of conveyor impact rollers is crucial for ensuring the efficiency and longevity of a conveyor system. Properly sized rollers help distribute the load evenly, reducing the risk of belt damage and system malfunctions. Incorrect sizing can lead to increased wear and tear, higher maintenance costs, and potential operational downtime. By matching the roller size to the specific requirements of the application, businesses can optimize material flow, enhance productivity, and minimize operational disruptions.
Guide to Choosing the Right Size
- Load Capacity: Determine the maximum load that the conveyor system will handle. The rollers must be able to support the weight without deformation or excessive wear. This involves calculating the combined weight of the transported materials and considering dynamic impacts.
- Roller Diameter: The diameter of the roller should be selected based on the load and belt speed. Larger diameters provide better load support and reduce rotational speed, which can minimize wear. Common diameters range from 89 mm to 159 mm, but the choice depends on specific operational needs.
- Roller Length: The length of the rollers should match the width of the conveyor belt to ensure even load distribution. Custom lengths can be made to fit unique conveyor designs and applications.
- Shaft Diameter and Bearing Size: Ensure that the shaft diameter and bearing size are compatible with the conveyor system. These components need to support the rotational forces and provide smooth operation. Standard sizes are often available, but custom options may be necessary for specific requirements.
- Environmental Conditions: Consider the operating environment, including temperature, humidity, and exposure to chemicals or abrasives. These factors influence the choice of materials and coatings for the rollers.
Customization Options
Customization options for conveyor impact rollers are available to meet unique operational requirements:
- Material Selection: While standard impact rollers may use steel or other metals, nylon rollers offer a lightweight, corrosion-resistant alternative that can be tailored to specific applications.
- Coatings and Treatments: Rollers can be coated with various materials to enhance their durability and resistance to environmental factors. For example, rubber or polyurethane coatings can improve impact absorption and reduce noise.
- Dimensions: Custom dimensions, including roller diameter, length, and shaft size, can be specified to fit non-standard conveyor systems or unique load conditions.
- Shock-Absorbing Elements: The type and arrangement of shock-absorbing materials, such as rubber rings or discs, can be customized to optimize impact absorption for specific applications.
Benefits of Nylon Material in Impact Roller Customization
Nylon offers several advantages when used in the customization of impact rollers:
- Durability: Nylon’s high tensile strength and wear resistance make it ideal for handling heavy loads and abrasive materials, extending the roller’s service life.
- Lightweight: Nylon rollers are significantly lighter than metal alternatives, making them easier to handle and install. This reduces labor costs and installation time.
- Corrosion Resistance: Nylon’s resistance to moisture and chemicals makes it suitable for use in harsh environments, such as mining and food processing, where exposure to corrosive substances is common.
- Low Friction: The low friction coefficient of nylon reduces energy consumption and wear on the conveyor belt, improving overall system efficiency and reducing operational costs.
- Noise Reduction: Nylon rollers operate quietly, which is beneficial in environments where noise reduction is important, such as manufacturing plants and distribution centers.
By carefully considering these factors and leveraging the customization options available with nylon materials, businesses can select the most appropriate conveyor impact rollers for their specific needs, ensuring optimal performance and longevity of their conveyor systems.
Conveyor Impact Roller Manufacturers
Market Leaders
Several companies have established themselves as market leaders in the production of conveyor impact rollers. These companies are recognized for their commitment to quality, innovation, and customer satisfaction. Among the most notable are:
- GRAM Conveyor: Known for its high-quality rollers and advanced manufacturing processes, GRAM Conveyor is a key player in the industry. They offer a wide range of conveyor rollers tailored to various applications, ensuring durability and efficiency.
- Damon Industry: With a global presence, Damon Industry is renowned for its comprehensive portfolio of conveyor rollers. Their products are used in numerous industries, from logistics to mining, demonstrating their versatility and reliability.
- Interroll Group: Interroll Group is another prominent manufacturer, offering a variety of conveyor rollers designed for different industrial applications. Their focus on innovation and sustainability sets them apart in the market.
Innovations and Technologies
Leading manufacturers are continuously innovating to improve the performance and efficiency of conveyor impact rollers. Some of the key advancements include:
- Smart Technology: Integration of smart sensors in rollers to monitor performance in real-time. These sensors can detect wear, temperature changes, and operational anomalies, allowing for predictive maintenance and reducing downtime.
- Advanced Materials: Development of new materials and composites, such as enhanced nylon blends, that offer superior strength, flexibility, and resistance to wear and environmental factors.
- Precision Manufacturing: Utilization of cutting-edge manufacturing techniques like CNC machining and automated assembly lines to ensure high precision and consistency in roller production.
- Eco-Friendly Solutions: Focus on sustainability by developing rollers made from recycled materials and implementing energy-efficient manufacturing processes.
Quality and Durability Considerations
When selecting a manufacturer for conveyor impact rollers, quality and durability are paramount. Key considerations include:
- Material Quality: High-quality raw materials, such as premium-grade nylon, are essential for producing durable and reliable rollers. Manufacturers should adhere to strict quality control standards to ensure material integrity.
- Manufacturing Standards: Companies that follow rigorous manufacturing standards and certifications (e.g., ISO) provide assurance of consistent product quality and performance.
- Testing and Validation: Reputable manufacturers conduct extensive testing and validation of their products, including load testing, impact resistance, and longevity trials, to ensure they meet industry standards and customer requirements.
- Customer Support: Excellent customer support and after-sales service are crucial. Manufacturers that offer comprehensive support, including installation assistance, maintenance services, and technical advice, add significant value to their products.
Leading Manufacturers of Nylon Conveyor Rollers
Several manufacturers are particularly noted for their expertise in producing nylon conveyor rollers:
- GRAM Conveyor: As a market leader, GRAM Conveyor excels in producing high-quality nylon rollers. Their products are known for their durability, low maintenance, and exceptional performance in various industrial applications.
- Damon Industry: Damon Industry offers a wide range of nylon conveyor rollers that are designed to meet the demanding needs of industries such as logistics, manufacturing, and food processing. Their focus on innovation ensures that their products remain at the forefront of the market.
- Interroll Group: Interroll Group’s nylon conveyor rollers are renowned for their precision engineering and robust construction. They are widely used in industries where high performance and reliability are critical.
- Rulmeca: Rulmeca specializes in producing rollers for heavy-duty applications, including nylon impact rollers. Their products are designed to withstand harsh environments and heavy loads, making them a preferred choice in industries like mining and construction.
By focusing on quality, innovation, and customer satisfaction, these leading manufacturers ensure that their nylon conveyor rollers meet the highest standards of performance and reliability. Businesses can rely on these manufacturers to provide the solutions needed to enhance the efficiency and longevity of their conveyor systems.
Maintenance and Care for Conveyor Impact Rollers
Routine Inspection and Maintenance
Regular maintenance and inspection are crucial for ensuring the optimal performance and longevity of conveyor impact rollers. Key steps include:
- Scheduled Inspections: Establish a routine inspection schedule to check for wear, alignment, and proper functioning of the rollers. Inspections should be conducted weekly or monthly, depending on the usage intensity and operating conditions.
- Cleaning: Keep the rollers clean from debris, dust, and other contaminants. Regular cleaning prevents buildup that can cause operational issues and increase wear on the rollers and conveyor belt.
- Lubrication: Ensure that the bearings and other moving parts are adequately lubricated to reduce friction and wear. Use appropriate lubricants recommended by the roller manufacturer.
- Alignment Check: Verify that the rollers are properly aligned with the conveyor belt to prevent uneven wear and potential damage. Misalignment can lead to increased friction and operational inefficiencies.
Troubleshooting Common Issues
Addressing common issues promptly can prevent minor problems from escalating into significant failures:
- Excessive Noise: Noise can indicate issues such as misalignment, worn bearings, or debris caught in the rollers. Inspect and rectify the root cause promptly.
- Roller Skipping or Slipping: This can be caused by improper tension in the conveyor belt or worn roller surfaces. Adjust the belt tension and replace rollers if necessary.
- Uneven Wear: Uneven wear on the rollers may result from misalignment or imbalanced loads. Check the alignment and load distribution, and adjust accordingly.
- Roller Jamming: Jamming can occur due to foreign objects or buildup within the roller system. Regular cleaning and inspections can help prevent this issue.
Extending the Lifespan of Rollers
To maximize the service life of conveyor impact rollers, implement the following practices:
- Preventive Maintenance: Regular preventive maintenance helps identify and address potential issues before they cause significant damage. This includes scheduled inspections, cleaning, and lubrication.
- Quality Components: Use high-quality rollers and replacement parts to ensure durability and reliable performance. Investing in quality components reduces the frequency of replacements and repairs.
- Proper Training: Ensure that personnel operating and maintaining the conveyor system are adequately trained. Proper handling and maintenance practices can significantly extend the life of the rollers.
- Environmental Control: Minimize exposure to harsh environmental conditions, such as extreme temperatures, moisture, and corrosive substances. Protective covers or enclosures can help shield the rollers from adverse conditions.
Maintenance Tips Specific to Nylon Impact Rollers
Nylon impact rollers have unique properties that require specific maintenance considerations:
- Temperature Monitoring: Nylon can be sensitive to extreme temperatures. Ensure that the operating environment remains within the recommended temperature range to prevent material degradation.
- Chemical Exposure: While nylon is resistant to many chemicals, prolonged exposure to certain substances can cause damage. Regularly inspect rollers for signs of chemical damage and avoid using harsh cleaning agents.
- Load Management: Avoid overloading the conveyor system. Although nylon rollers are durable, excessive loads can lead to premature wear and deformation.
- Replacement Timing: Monitor the condition of nylon rollers closely and replace them at the first signs of significant wear or damage. Timely replacement prevents further damage to the conveyor system and ensures continuous operation.
By adhering to these maintenance practices, businesses can ensure the reliable performance and extended lifespan of their conveyor impact rollers. Proper care and routine inspections not only enhance operational efficiency but also reduce maintenance costs and downtime, contributing to overall productivity.
HOME IMPROVEMENT
Enhancing Quality of Life: Simple Wellness Routines for Seniors
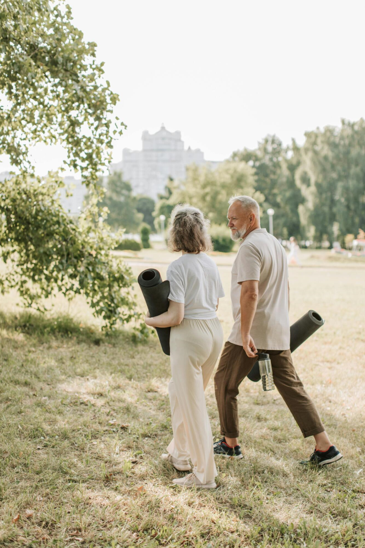
Getting older doesn’t mean slowing down completely-it just means finding new ways to care for your body, mind, and spirit. Every small step you take adds up to a stronger, more joyful quality of life. From morning stretches to quiet moments in nature, simple routines can bring comfort, stability, and strength at any age.
If you’re looking for easy ways to feel better each day, there’s good news. Wellness is not hard; it simply requires consistency. Keep reading to discover routines that support seniors in feeling their best without adding stress or pressure. Read on.
Start the Day with Gentle Movement
Mornings are the perfect time to wake up the body with light movement. Stretching helps with flexibility, balance, and blood flow. Even a five-minute walk around the house or gentle yoga poses can boost energy and ease stiffness.
These small habits build strength over time and reduce the risk of falls or joint pain. They also set a positive tone for the day ahead. The key is to move in a way that feels good and to do it often.
Nourishment with Purpose
As we age, our bodies need more care and attention when it comes to food. A balanced diet full of fiber, healthy fats, and protein supports energy, digestion, and mental clarity. Drinking plenty of water also helps keep the body running smoothly.
Meals can be simple; variety, color, and fresh ingredients are what matter. Many seniors find joy in preparing simple meals that are both comforting and nourishing. Eating well supports not just physical health but also mood and memory.
The Power of Rest and Routine
Sleep is essential at every stage of life. For seniors, creating a bedtime routine can help improve the quality of rest. That might mean reading, dimming the lights, or enjoying calming music before sleep.
Daily structure also brings peace of mind. Knowing what to expect each day can help reduce worry, especially for those adjusting to retirement or changes in lifestyle. A regular rhythm makes space for calm and clarity.
Mental Wellness Matters
Staying mentally active is just as important as physical care. This might mean reading, doing puzzles, or enjoying hobbies that spark curiosity. Social connection is key too. Conversations with friends, family, or community groups can brighten a day and reduce feelings of isolation.
Simple techniques like breathing exercises, journaling, or time outdoors are helpful in managing stress and anxiety in seniors. These quiet moments give space to recharge and stay grounded, even when life feels uncertain.
Enhancing Quality of Life: Simple Wellness Routines for Seniors
Living well as a senior isn’t about doing everything at once. It’s about making choices each day that bring comfort, balance, and joy. A short walk. A healthy snack. A phone call with a friend. These small actions build a quality of life that feels full, steady, and strong.
You don’t have to change everything overnight. Start with one small routine, and build from there. With time, these moments will shape days that feel lighter, brighter, and more connected. Wellness is always within reach one step at a time.
HOME IMPROVEMENT
Methods to Speed Up Water Damage Restoration in Your Property
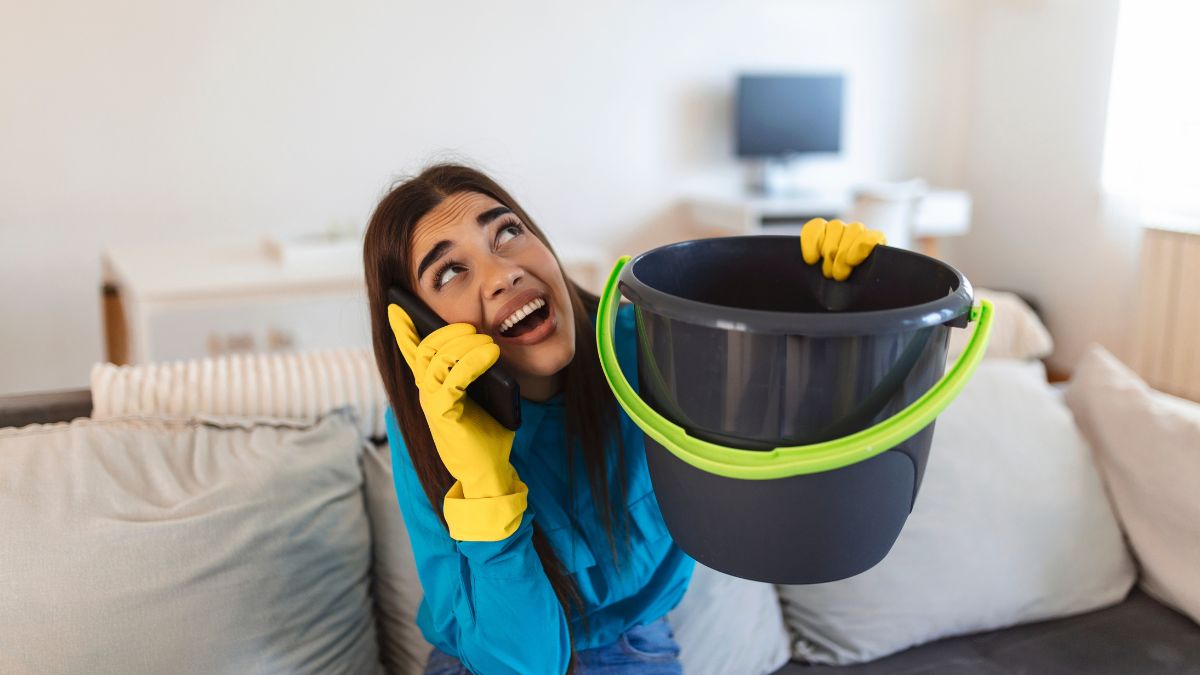
Water damage can occur in various ways, such as from floods, plumbing failures, and natural disasters. When water intrudes into your property, the urgency to mitigate its effects is paramount. The longer water sits, the more severe the damage can become, leading to mold growth, structural issues, and increased restoration costs. Understanding effective methods for speeding up the water damage restoration process will protect your investment and create a safer living environment.
Assess the Damage Quickly
Assessing the damage swiftly is crucial in initiating the restoration process. The faster you identify the type and extent of the water intrusion, the quicker you can create an actionable plan. Utilize a visual inspection to identify the source of the water and the areas most affected. Engage professionals to conduct a thorough assessment if the damage seems significant. They often utilize moisture detection tools to determine hidden water pockets that could lead to further issues if overlooked.
Addressing the source of the water first prevents additional damage, making it essential to understand whether the situation is due to a burst pipe or a more extensive flooding incident. Implementing prompt communication with your insurance provider can facilitate effective mitigation efforts. Make sure to document all damage with photographs, which can streamline the claims process.
Contact Water Damage Professionals
Once you’ve assessed the situation, contacting qualified water damage restoration professionals is a vital step. Their expertise ensures that restoration efforts proceed efficiently, saving you time and potential headaches. Water damage restorers possess specialized equipment and knowledge to effectively remove excess water, dry out materials, and sanitize the area. This action minimizes the risk of mold growth, which can start within 24 to 48 hours of water exposure.
Engaging professionals guarantees that the job adheres to industry standards and reduces the likelihood of future problems arising. Not all restoration companies are created equal; it’s beneficial to do some research and find one with positive reviews and the necessary certifications. Some companies offer advanced flood restoration, which incorporates modern techniques and technology designed to optimize the restoration timeline. Choosing experienced professionals can significantly reduce recovery time and enhance the effectiveness of the process.
Implement Proper Water Removal Techniques
Effective water removal techniques can dramatically influence the duration of the restoration process. By using industrial-grade water extraction equipment, you can rapidly eliminate standing water from the affected areas. This process typically involves the use of powerful pumps and vacuums to ensure thorough removal. Manual efforts, such as mopping and using towels, can support the extraction but should not be relied upon exclusively.
Clearing the water promptly protects your property and significantly reduces the potential for mold development and structural damage. To optimize this process, ensure that you are wearing protective gear like gloves and masks to avoid health risks. Pay attention to both visible and hidden areas, including carpets, under furniture, and inside walls, as these spaces may retain water. Quick action concerning water extraction can help speed up the restoration timeline.
Effective Drying Techniques Post-Water Removal
Once water has been removed, drying the affected areas becomes a top priority. Adequate drying can be achieved through several methods and tools, such as air movers and dehumidifiers, to ensure that moisture does not linger and cause further complications. Air dryers circulate air and promote evaporation, while dehumidifiers reduce humidity levels in the room. Proper ventilation will help to refine the process further; consider opening windows and doors to allow fresh air circulation.
You might need to aim for longitudinal drying, which includes drying materials at a slow and steady pace to prevent structural warping or damage. Make sure to regularly check humidity and moisture levels during this phase with a hygrometer, ensuring that they reach acceptable levels. Implementing effective drying techniques ensures that the space is safe and habitable once restoration is complete.
Evaluate and Repair Structural Issues
Post-drying evaluation of your property’s structure is necessary to identify any damage that remains. Carpets, drywall, and insulation may face considerable harm and require repair or replacement. Pay particular attention to subfloors, as water intrusion often compromises their integrity. Hiring qualified contractors for repairs helps ensure that work adheres to necessary building codes and standards.
Addressing structural issues promptly prevents them from escalating into larger problems. Any signs of mold or mildew should be dealt with immediately, as these can negatively affect air quality and your health. Once all repairs are assessed, a thorough inspection should confirm that the property is safe for occupancy before moving back in.
Prevent Future Water Damage
Preventing future water damage is about restoring the current situation and ensuring it does not happen again. Regular maintenance checks, such as clearing gutters, inspecting roofing, and ensuring proper drainage, can significantly reduce the chances of future water intrusions. Installing a sump pump and water alarms can alert you to potential problems early.
Developing a comprehensive emergency plan, including having contact information for restoration professionals, will yield peace of mind. Engage in ongoing property assessments regularly, as a proactive approach can identify vulnerabilities before they result in issues. Taking these preventive measures can help secure your investment for years to come.
By assessing the damage, contacting professionals, employing effective removal and drying techniques, evaluating structural integrity, preventing future issues, and maintaining communication with insurance personnel, you can significantly minimize the emotional and financial impacts of such unfortunate situations.
HOME IMPROVEMENT
Reasons to Invest in High-Quality Exterior Paint
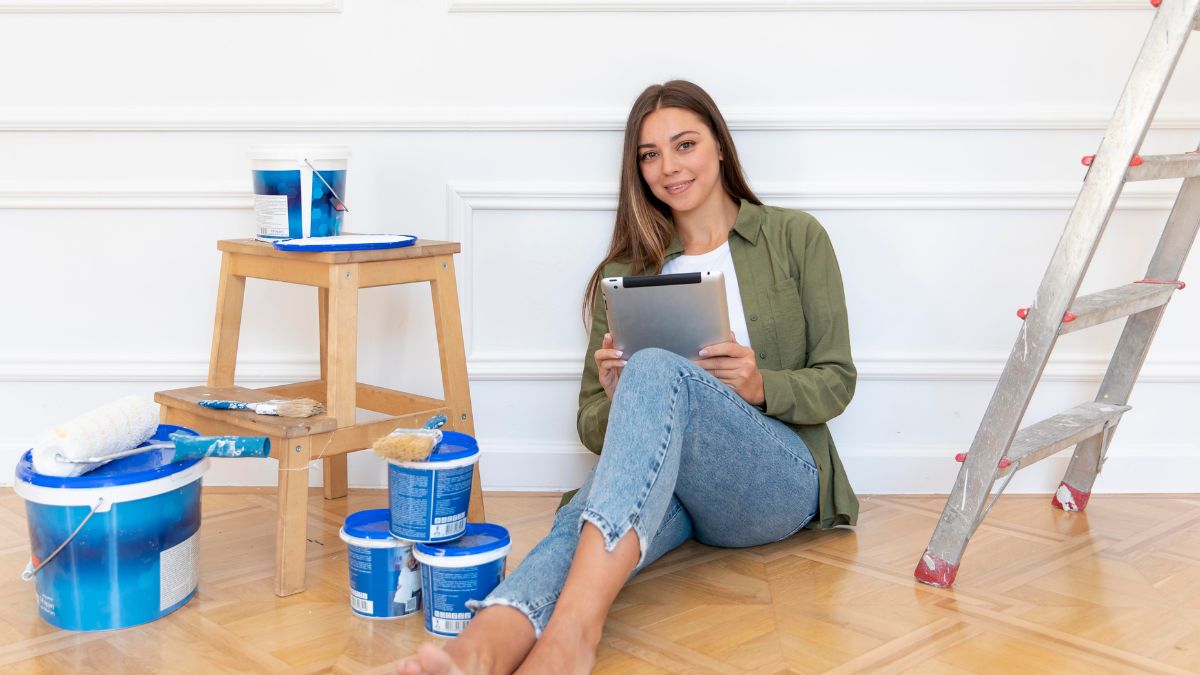
Every home speaks through its exterior. The walls, siding, and trim not only serve as a barrier from the elements but also shape first impressions. A well-kept exterior signals attention to care and longevity, while faded or peeling paint hints at neglect. The decision to invest in high-quality exterior paint can affect not just how a house looks, but how well it holds up over time. Beyond appearance, this choice has implications for property value, structural integrity, and ongoing maintenance costs. Selecting the right paint means thinking beyond color, it involves recognizing the role that quality plays in protection, performance, and durability.
Longer Lasting Protection
A major concern for any homeowner is how often the exterior of their house needs to be repainted. Climate, sun exposure, and moisture levels can all wear paint down far sooner than expected. When lower-grade paint is used, this wear accelerates, often resulting in chipping, cracking, or discoloration within just a few seasons. Higher-quality paint, by contrast, has a denser pigment load and more durable resins that better withstand UV rays, rain, wind, and temperature shifts. These features help extend the lifespan of your exterior paint, giving you more years between repainting and reducing long-term upkeep. With fewer repainting cycles required over the life of a home, the added cost of premium paint becomes a practical investment.
Improved Color Retention and Finish
When freshly applied, most paints look vibrant and smooth. The difference becomes clear over time. Inexpensive paint tends to fade faster, often turning chalky or uneven as pigments degrade. Quality paint includes advanced technology designed to hold color and resist fading, even after years under intense sunlight or harsh seasonal changes. This means the look chosen during application will stay closer to its original shade, resisting the washed-out or yellowed effect that can appear on cheaper coatings. A stable, consistent finish not only maintains curb appeal but also reflects better on property maintenance, whether for resale or personal pride.
Better Resistance to Weather and Environmental Stress
Exterior paint needs to hold up against far more than just sun and rain. Snow, frost, salt spray, mildew, and pollution all put pressure on a building’s surface. A low-grade paint can become brittle in cold weather or sticky in the heat, expanding and contracting unevenly, which may lead to cracks or peeling. On the other hand, high-quality exterior paints are engineered to adapt to seasonal changes. They form flexible, breathable films that move with the material underneath, whether it’s wood, brick, or siding. This adaptability prevents moisture from getting trapped, which reduces the risk of mold or rot and lowers the chances of costly structural repairs.
Stronger Adhesion and Coverage
Many assume that all paint covers a surface in the same way. This isn’t the case. Lower-end paints often require more coats to achieve the same opacity and finish, and even then, they might not adhere evenly. High-grade paint contains a richer concentration of solids, which are the binders and pigments that remain after the solvent evaporates. This means better coverage per gallon and less paint needed overall. With stronger adhesion, it clings to surfaces more effectively, reducing flaking and blistering over time. The end result is a smoother, more uniform appearance that lasts longer and looks more professional from the first application.
Lower Long-Term Maintenance Costs
A fresh coat of paint might seem like a cosmetic upgrade, but over time, it becomes a layer of protection that can help prevent damage. Poor-quality paint may save money upfront, but it often leads to more frequent touch-ups, repairs, or full repaints. These repeated jobs increase labor costs and consume time that could be spent elsewhere. On the other hand, higher-quality paint minimizes the need for ongoing maintenance. Its resistance to cracking, fading, and mildew cuts down on cleaning and repairs. With better durability, homeowners can wait longer before repainting, which leads to meaningful savings over the life of the home. For anyone thinking beyond the short term, the reduced cost of maintenance becomes a compelling reason to choose quality from the start.
Increased Property Value and Buyer Appeal
First impressions matter when selling a house. A well-maintained exterior, coated in long-lasting, rich-colored paint, can elevate the perception of the entire property. Buyers often view the condition of the paint as an indicator of how well the home has been cared for overall. When the exterior appears fresh and solid, it can increase interest and shorten time on the market. While it’s difficult to quantify the exact return on investment from high-quality paint, homes with professional finishes tend to show better and sell faster. The money spent upfront can translate into higher offers or smoother negotiations. Even if a sale isn’t imminent, a well-kept exterior reflects pride in ownership and adds lasting visual appeal to the neighborhood.
Choosing high-quality exterior paint is about far more than color choice or brand recognition. It’s a decision that influences how long a home looks its best, how well it’s protected, and how much maintenance will be required in the years ahead. A better paint today means fewer worries tomorrow, and a home that holds its strength and style, season after season.
- Cartoon1 year ago
Unlocking the Potential of Nekopoi.care: A Comprehensive Guide
- Game1 year ago
Exploring Aopickleballthietke.com: Your Ultimate Pickleball Destination
- BUSINESS1 year ago
What Companies Are In The Consumer Services Field
- BUSINESS1 year ago
Unraveling the Mystery of 405 Howard Street San Francisco charge on Credit Card
- HOME IMPROVEMENT1 year ago
Vtrahe vs. Other Platforms: Which One Reigns Supreme?
- TECHNOLOGY1 year ago
The Guide to Using Anon Vault for Secure Data Storage
- ENTERTAINMENT11 months ago
Understanding Bunkr Album: A Comprehensive Guide
- ENTERTAINMENT1 year ago
The Epic Return: Revenge of the Iron-Blooded Sword Hound