TECHNOLOGY
Understanding Scrubber Tower: The Key to Clean Air in Industrial Processes
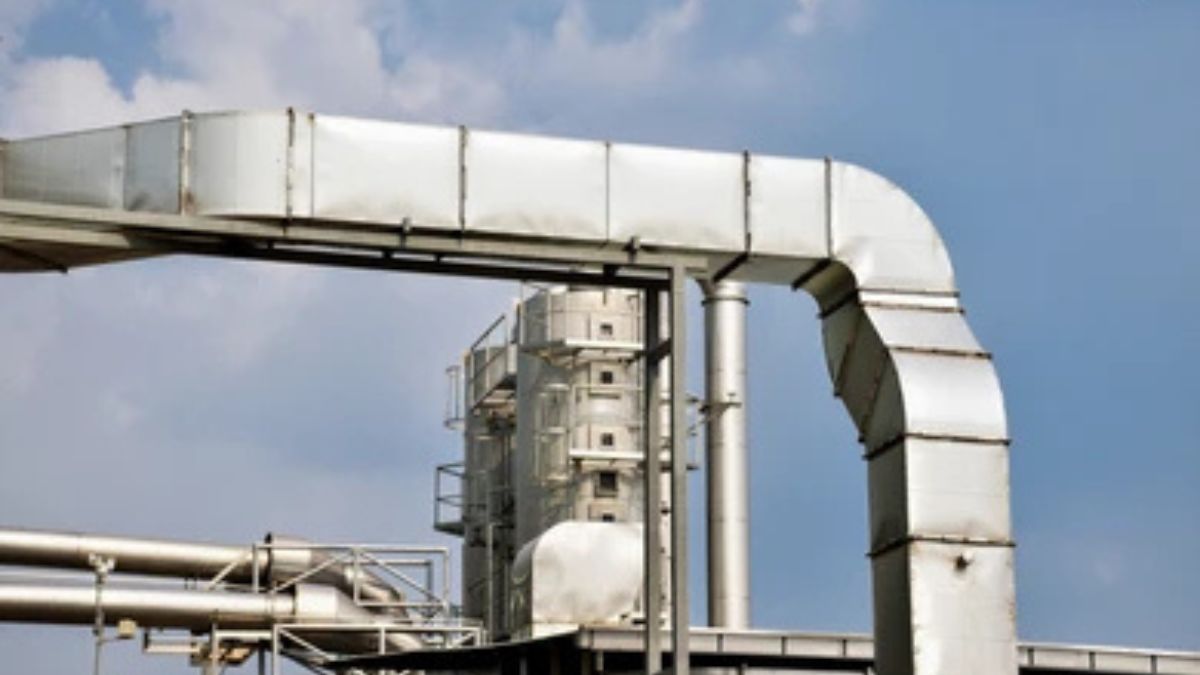
Air pollution is a pressing concern in today’s industrial landscape. Factories and manufacturing units emit various pollutants that can severely impact both the environment and public health. As industries strive to meet regulatory standards, solutions for cleaner emissions have become more critical than ever.
Enter the scrubber tower, a revolutionary technology designed to purify air from harmful contaminants. These systems play an essential role in ensuring that industries operate sustainably while protecting our planet’s atmosphere. Understanding how scrubber towers function and their importance could be your key to appreciating clean air initiatives within industrial processes.
Let’s dive into what makes these impressive structures vital players in maintaining environmental integrity!
What is a Scrubber Tower and How Does it Work?
A scrubber tower is an essential piece of equipment in industrial air pollution control. It operates by removing harmful pollutants from exhaust gases before they are released into the atmosphere.
The process begins when contaminated air enters the scrubber tower. As the air flows through, it encounters a scrubbing liquid, typically water or a chemical solution. This liquid captures and neutralizes harmful substances.
Packed tower scrubber utilize packing materials inside the tower to enhance contact between gas and liquid. These materials create more surface area for better absorption of pollutants, making them highly efficient.
As air continues its journey upward through the packed layers, cleaner air emerges at the top while contaminants remain trapped within the scrubbing solution. This efficient design helps industries meet stringent environmental regulations while promoting cleaner operations.
Types of Scrubber Towers
Scrubber towers come in various designs, each tailored for specific applications and pollutants. The most common type is the packed tower scrubber. This design utilizes packing materials that increase surface area, facilitating better contact between gas and liquid.
Another popular variant is the tray scrubber. It employs a series of trays to promote gas-liquid interaction, making it effective for larger volumes of air pollution control.
Venturi scrubbers offer a different approach by using high-velocity jets to atomize the scrubbing liquid, creating an intense mixing action ideal for particulate removal.
For specialized needs, electrostatic scrubbers utilize electrical fields to charge particles, allowing them to be attracted to collection plates. Each type serves its purpose effectively while helping industries meet environmental regulations. Understanding these variations can help companies choose the right system for their unique challenges in air quality management.
Benefits of Using Scrubbers in Industrial Processes
Scrubber towers play a vital role in reducing air pollution. They capture harmful gases and particulates, ensuring cleaner emissions. This process not only improves air quality but also meets regulatory standards.
Using scrubbers can lead to significant cost savings for industries. By minimizing the release of pollutants, companies often avoid hefty fines associated with non-compliance. Additionally, they might see reduced costs related to health care and environmental cleanup.
Another benefit is enhanced worker safety. Cleaner air translates to a healthier work environment, boosting employee morale and productivity. Workers are less likely to experience respiratory issues when exposed to filtered air.
Moreover, many modern scrubber designs are energy-efficient. They optimize resource use while maintaining effectiveness in pollutant removal—an essential feature for sustainable operations in today’s eco-conscious climate.
Investing in scrubber technology promotes not just compliance but also corporate responsibility toward environmental stewardship.
Common Industries That Use Scrubber Towers
Scrubber towers play a crucial role across various industries. They are essential in sectors like chemical manufacturing, where controlling emissions is vital for compliance.
The oil and gas industry heavily relies on scrubbers to manage volatile organic compounds during extraction processes. These systems help reduce harmful pollutants released into the atmosphere.
Power generation facilities also utilize packed tower scrubbers. They effectively remove sulfur dioxide from flue gases, ensuring cleaner air output from energy production.
In the food processing sector, scrubber towers aid in eliminating odors and particulates that can arise during production. Maintaining air quality enhances worker safety and comfort.
Additionally, metal fabrication plants use these systems to control dust and fumes generated by welding or cutting processes. This not only protects workers but also meets environmental regulations.
Maintenance and Upkeep of Scrubber Towers
Regular maintenance is crucial for the effective operation of scrubber towers. Over time, contaminants can build up in the system, potentially leading to reduced efficiency. Scheduling routine inspections helps identify any issues before they escalate.
Cleaning components like packing media is essential. This not only enhances performance but also prolongs the lifespan of the equipment. Using appropriate cleaning agents ensures that no harmful residues remain post-maintenance.
Another key aspect involves monitoring operational parameters. Keeping an eye on flow rates and pressure differentials allows operators to catch deviations early, ensuring optimal functionality.
Documentation plays a significant role too. Maintaining accurate records of all maintenance activities aids in tracking performance trends and compliance with environmental regulations.
Training staff thoroughly on operating procedures fosters a proactive approach to upkeep. Empowered employees help maintain air quality while maximizing productivity within industrial processes.
The Future of Clean Air in Industrial Processes
As industries evolve, so does the technology surrounding air purification. Innovations in scrubber tower design are leading the charge toward cleaner emissions. The integration of advanced materials and smart monitoring systems is making these towers more efficient than ever.
Sustainability is becoming a core focus for many manufacturers. They are actively seeking solutions that not only comply with regulations but also enhance environmental responsibility. This shift drives investment into research and development for better scrubber technologies.
Moreover, there’s a growing trend towards automation within industrial processes. Automated scrubbers can adapt to fluctuating operational conditions, ensuring optimal performance at all times.
Public awareness around air quality continues to rise. As consumers demand greener practices from companies, businesses will need to prioritize clean air initiatives as part of their commitment to sustainability. Embracing innovation today shapes a healthier tomorrow for everyone involved in industrial sectors.
Conclusion
Scrubber towers play a crucial role in combating industrial air pollution. As industries continue to grow, so does the need for effective air purification systems. The use of scrubber towers, especially packed tower scrubbers, provides an efficient solution to meet environmental regulations and improve air quality.
With various types available—each tailored for specific pollutants—companies have options that best fit their operational needs. The benefits are clear: reduced emissions, compliance with laws, and enhanced workplace safety. Many sectors including manufacturing, chemical processing, and power generation leverage these technologies to maintain cleaner environments.
To ensure optimal performance from scrubber towers, regular maintenance is essential. This proactive approach not only extends the lifespan of these systems but also maximizes their efficiency in removing harmful substances from the air.
As we look ahead, advancements in technology promise even more innovative solutions for ensuring clean air within industrial processes. With growing awareness about environmental responsibility and health concerns related to poor air quality, the future appears bright for scrubber tower applications across various industries.
The importance of integrating effective scrubbing systems cannot be overstated as businesses strive toward sustainability while fulfilling regulatory requirements. Clean air is vital—not just for today’s workforce but also for generations to come.
TECHNOLOGY
Technologies That Are Reshaping Pumping Operations in Multiple Sectors
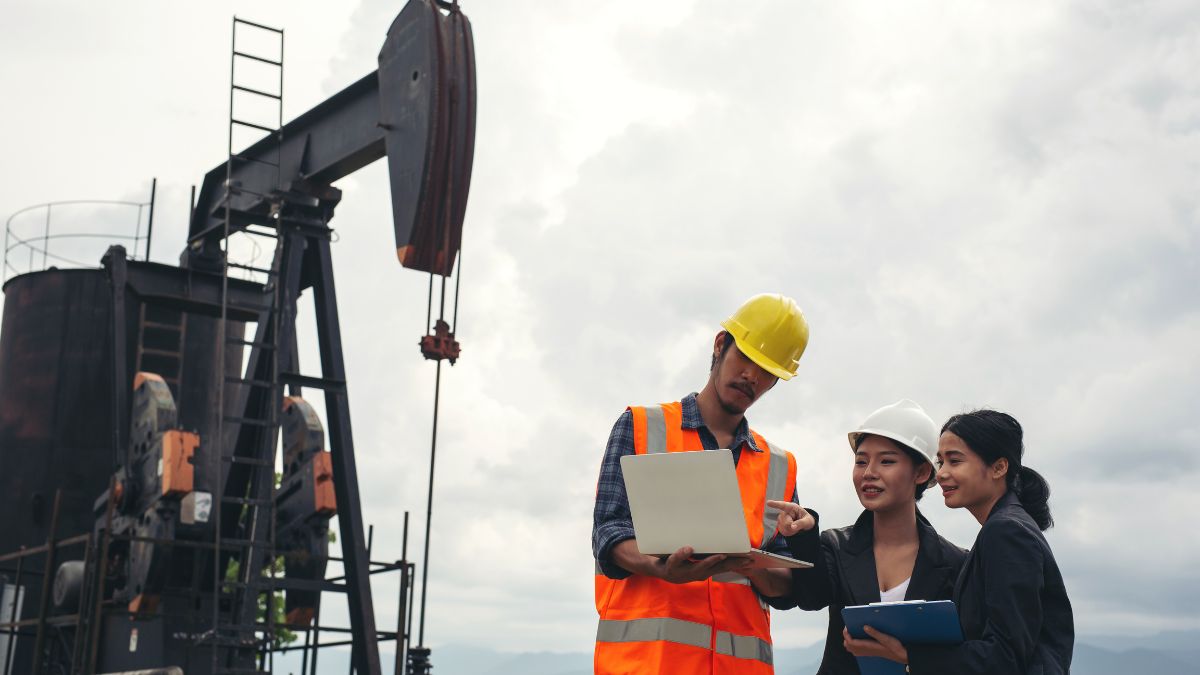
Across construction sites, oil fields, wastewater treatment plants, and mining operations, pumping systems form the backbone of fluid transfer. Once considered basic mechanical workhorses, today’s pumps have evolved into intelligent, efficient, and highly specialized tools powered by cutting-edge technology. From smart sensors to automation and material innovation, the transformation of pumping operations is improving performance, safety, and sustainability in every industry they touch.
The shift is more than a matter of replacing older equipment with newer models. It represents a rethinking of how fluids are managed in challenging environments, making systems more adaptive, resilient, and cost-effective. With technology driving this evolution, operators are achieving better control, reduced downtime, and superior outcomes at scale.
Smart Pumps and Digital Integration Are Becoming the Norm
One of the most notable shifts in the pumping industry is the rise of smart pump systems. These machines are embedded with sensors, connectivity modules, and integrated controllers that monitor performance in real time.
Rather than waiting for failure or relying on periodic inspections, operators can now detect pressure drops, flow inconsistencies, and mechanical wear before they result in costly disruptions. Leading platforms like https://www.daepumps.com/ and similar commercial pump providers are now offering fully integrated systems with remote monitoring dashboards. These solutions allow engineers and maintenance teams to track operational metrics from anywhere, often with predictive analytics that alert them to potential issues. It’s a proactive approach to fluid management that reduces emergency repairs, extends equipment life, and increases energy efficiency.
Integration with SCADA (Supervisory Control and Data Acquisition) systems allows pumping operations to be part of broader infrastructure management. For municipalities, mining facilities, or agricultural enterprises, this level of digital control enhances planning, boosts uptime, and supports scalable operations.
Variable Frequency Drives (VFDs) Enable Energy Optimization
Energy consumption is one of the most significant costs in any fluid handling system. Traditional pumps often run at full speed, regardless of actual demand, resulting in wasted energy and excessive wear. Variable frequency drives (VFDs) change that equation by adjusting the motor’s speed to match real-time flow and pressure needs.
By dynamically controlling motor speed, VFD-equipped pumps improve energy efficiency by up to 50% in some applications. This reduces utility bills and lowers greenhouse gas emissions, an increasingly important factor for industries focused on sustainability.
In wastewater treatment and HVAC systems, VFDs allow operators to fine-tune pump output based on water demand or temperature fluctuations. In mining or oil and gas, they provide the flexibility to adjust to changing load conditions without halting production. The result is a more responsive, cost-effective system that aligns with operational and environmental goals.
Corrosion-Resistant Materials Improve Longevity
Pumps operating in harsh environments, such as chemical processing plants, marine operations, or mining facilities, are exposed to highly abrasive and corrosive fluids. Advances in materials science have led to the development of new pump components that are more durable and resistant to degradation.
Thermoplastics, stainless steel alloys, and ceramic-coated components now offer enhanced protection against chemical attack, abrasion, and extreme temperatures. These materials extend service life, reduce maintenance intervals, and help prevent costly shutdowns due to part failure.
In sectors where downtime can lead to massive financial losses, the use of advanced materials is no longer optional; it’s a requirement. With pumps designed to endure the toughest conditions, companies can operate with greater confidence and reliability, even in the most demanding environments.
Automated Priming and Self-Regulation Reduce Manual Intervention
Traditional pumping systems often require manual priming, startup procedures, or adjustments to flow settings. These tasks consume labor and introduce the risk of human error. Today’s automated pumps include self-priming features, built-in diagnostics, and flow adjustment algorithms that make operations significantly more efficient.
Self-regulating systems are valuable in multi-pump setups or locations with limited personnel, such as remote agricultural fields or offshore installations. The pump automatically calibrates its output to match demand and adjusts when conditions change, such as when additional pumps come online or fluid viscosity fluctuates.
These systems monitor critical variables like temperature, vibration, and torque, providing early warnings before performance drops. By minimizing the need for hands-on operation, they improve safety and allow staff to focus on higher-value tasks.
Modular and Custom Configurations Enhance Flexibility
Industries increasingly demand pumping solutions that can be adapted to unique constraints, whether it’s limited space, fluctuating flow rates, or mobile deployment. Modular pump systems, which allow operators to swap or upgrade components without replacing the entire unit, offer unparalleled flexibility.
These configurations can be scaled up for large operations or downsized for precision applications. A construction firm might use modular dewatering pumps during rainy seasons, while a chemical plant might need a custom setup for transferring volatile compounds under specific conditions.
Pumping technology is evolving at a rapid pace, driven by the need for efficiency, durability, and intelligence. Whether you’re managing a municipal water network, a mining operation, or an industrial processing facility, these innovations are redefining what’s possible. From smart monitoring to advanced materials and energy-saving designs, modern pumps are more than just machines; they’re critical components in a smarter, more sustainable infrastructure. Investing in the right technologies today means more reliable operations, lower costs, and greater resilience for tomorrow’s demands.
TECHNOLOGY
Top Sheet Metal Fabrication Companies In China, USA & Europe
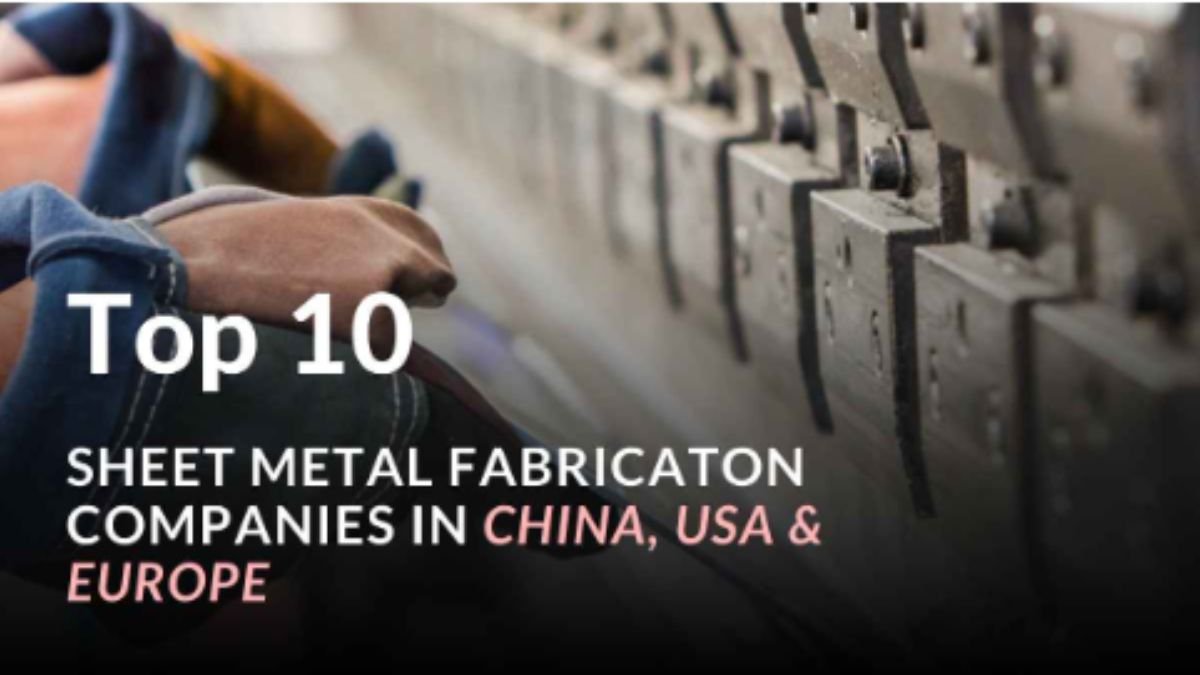
Finding the right sheet metal fabrication companies for your project is a challenging job. The choice to perform fabrication in-house or to hire outside vendors to provide comprehensive fabrication services is predicated on considering quality, volume, capacity, need, and project specifications. Fret not; we have narrowed down your search a bit and enlisted the leading 10 sheet metal processing companies across the world. These companies are capable of precisely handling small to medium-sized productions.
As part of this guide, we identified the prominent players of custom sheet metal fabrication, their specialization, service offerings, and strengths. So, keep on reading to figure out which company would be most suited to fulfill your needs.
Rank #01: ProleanTech
Year Established: 2009
Address: 815 ZhongYang Building, No.24 Fuhai Road Fuyong Community, Baoan District, Shenzhen, China
Employee Size: 11-50
Website: www.proleantech.com
Company Overview:
Prolean Tech is among the prestigious sheet metal fabrication companies. The company provides clients with precise sheet metal products made from aluminum, food-grade stainless steel, and copper alloys. Their products adhere to ISO 9001:2015. Proleans’ in-house capability is capable of meeting diverse market demands for both low and high-production volumes. A very unique benefit of Prolean Tech is its AI-powered online quoting system.
Metal Fabrication Services
- Laser Cutting (up to 25 mm thickness, 1500 x 3000 mm cutting area)
- CNC Punching (high-volume punching, complex holes/patterns)
- Bending (up to 6 mm thickness, high precision, accurate bend angles)
- Waterjet Cutting (up to 100 mm thickness, 3000 x 6000 mm cutting area)
- Welding (MIG, TIG, Spot Welding)
- Stamping & Rolling (large volumes of complex shapes, accurate cylindrical bending)
- Finishing Treatments (Powder Coating, Anodizing, Plating, Deburring)
Companies Served
Prolean Tech operates globally, providing services to sectors such as:
- Automotive
- Aerospace
- Medical Devices
- Electronics
- Construction
- Consumer Products
Read More: Aerospace Sheet Metal Fabrication
Why Prolean Tech Is Your Go-To Partner For Fabrication Project?
Being a precision-driven, holding state-of-the-art machines to deliver its services in the minimal time possible, Prolean is your reliable provider for any form of sheet metal fabrication.
From prototype through to low to high-run applications, Prolean Tech guarantees optimal production to meet your precise requirements.
More benefits of working with Prolean include;
- Precision Fabrication: (Custom, thick, and thin specification or tight tolerances)
- Diverse Material Options: Quality-oriented, stainless steel, copper, titanium, chromium, and many More.
- Fast Turnaround: Lead times involved are in the range of a single day.
- ISO Certified: Quality-oriented with ISO 9001:2015 certification policy.
- Global Clientele: For clients in the automotive and quickly, aerospace, electronics, and construction industries, and all other related sectors.
If you are looking for top sheet metal fabrication companies in China, Prolean Tech is your one-stop shop for all custom projects, and you can contact them for a free instant quote.
Rank #02: KMF Metals
Year Established: 1971
Address: Office: High Carr Business Park, Millennium Way, Newcastle ST5 7UF, United Kingdom.
Employee Size: 501-1K employees
Website: www.kmf.co.uk
Core Business Capabilities:
- CNC Punching
- Laser Cutting
- Metal Forming
- Welding: (MIG/TIG welding, stud welding, spot welding)
- Powder Coating
- Metal Finishing: (Services in concern include powder coating, painting, bead blasting, graining, and silk screening)
- Product Assembly and Integration:
- Stainless Steel Fabrication: (Separate storage for non-ferrous and rust-resistant pieces)
- Quality and Inspection: ISO 9001:2015, and AS9100 which guarantee UK-based traceability to the highest standard)
- CAD Design and Engineering
Company Overview:
KMF Metals is a UK-based sheet metal custom fabrication company providing services to industries for over 2 decades. They serve the automotive, telecom, and equipment energy sectors. KMF has a next-generation facility manufacturing space of over 255,000 sq. ft, wherein KMF functions 24/7 and uses equipment like Trumpf, Salvagnini, and Gema powder coaters, etc.
The company’s products adhere to quality standards such as ISO 9001: 2015, and AS9100 certifications. Moreover, they offer businesses across industries a range of custom metal fabrication services. KFM integrates advanced IT solutions for meeting short deadlines, and overcome production challenges.
Benefits of Working With KMF Metals:
- End-to-End Services: From Design to End-User Product
- Industry-Leading Technology: (Technologically advanced defensive machines for CNC punching, laser sheet cutting, etc)
- Advanced Quality Assurance: (Operating as an ISO 9001:2015 and AS9100 company for the best quality assurance)
- Global Capabilities: Fabrication in the United Kingdom and Europe for worldwide original equipment manufacturers and companies.
Companies Served
KFM Covers industries including;
- Aerospace
- Defense
- Automotive
- Food processing, and many more.
KMF Metals provides original, affordable, and fast sheet metal fabrication services to companies that seek dependable, customized solutions.
Rank #03: KDM Fabrication
Established Year: 2008
Country: China
Address: 9 Xinyuan Road, Huishan District, Wuxi City, Jiangsu Province, China.
Employee Size: 50-200
Core Business Capabilities:
- Sheet Metal Production (Stainless steel, copper, aluminum, galvanized steel)
- Cutting (Waterjet, sawing, shearing)
- Bending (Metal brake, bending machines)
- Welding (TIG, MIG, laser welding)
- Surface Treatment (Buff polished hing, powder coating, sandblasting, ng)
Company Overview:
KDM Fabrication lies among pioneering China sheet metal fabrication companies. It specializes in sheet metal production for the automotive, medical, electronics, and electric power industries. They offer a wide selection of metal sheets, including stainless steel, copper, and aluminum.
With services like waterjet cutting, MIG and TIG welding, and powder coating, KDM ensures precision and quality. Their experienced team delivers reliable, high-quality metal parts that are built to last.
Rank #04: Morton Industries
Established Year: 1946
Country: United States
Address: 70 Commerce Dr, Morton, IL, 61550, United States of America.
Employee Size: 501-1K employees
Core Business Capabilities:
- Laser Sheet Cutting
- Sheet Metal Enclosures
- Bending Alloys
- Fabricated Tube Assemblies
- Pack-Out Services
- General Sheet Metal Manufacturing
Company Overview:
Morton Industries is a leading US-based OEM manufacturer of sheet metal fabrication serving over eight decades. The company provides products for automobile, mining, construction, agriculture, and military industries.
Morton Industries is focused on providing alloy manufacturers with affordable and efficient services using the latest tools and expertise. Their core sheet metal services are ISO oriented and compliant with standards ISO 9001 accreditation. So, the quality of the products manufactured by the company is always smooth and the operations are efficient.
Morton Industries is a reliable manufacturing company that serves small and large enterprises.
Key Industries Served:
- Mining
- Construction
- Agriculture
- Automotive
- Power Sports
- Military
Rank #05: Estes Design and Manufacturing
Established Year: 1976
Country: United States
Address: 470 S. Mitthoeffer Rd. Indianapolis, IN 46229
Employee Size: 51-200
Core Business Capabilities:
- 3D Laser Welding & Accelerators
- Prototyping
- Sheet Metal Fabrication
- Light Guage Sheet Metal Fabrication (especially carbon steel, stainless steel, & aluminum)
Company Overview:
Estes Design and Manufacturing, Inc. is among the premier custom sheet metal fabricators that make custom parts for various industries. As a sheet metal manufacturer specializing in 3D laser welding and prototyping, the company provides super-quality products that adhere to ISO 9001 & 13485.
It focuses on the value addition of light sheet metals of aluminum, stainless, and carbon steel. Estes can fully customize thread rollers, including changes in thickness, length, surface treatment, and material type based on customer needs.
Key Industries Served:
- Medical Equipment
- Aerospace
- HVAC
- Appliances
- Furniture Manufacturing
Rank #06: Prototek Manufacturing, LLC
Established Year: 1987
Country: United States
Address: 244 Burnham Intervale Road, Contoocook, New Hampshire 03237 USA
Quality Assurance: AS9100D Certified, ISO 9001:2015, ISO 13485:2016, & ITAR
Employee Size: 200-500
Core Business Capabilities:
- Sheet Metal Fabrication
- Laser Metal Sheet Cutting
- Water Jet Sheet Metal Cutting
- Welding & Grinding
- Sheet Metal Finishes (Painting, Powder Coating, Polishing, and Anodizing)
- Forming & Drilling
- Mechanical Assembly
Company Overview:
Prototek Manufacturing, LLC is a US-based company, founded in 1987. It has a skilled engineering team specializing in project design and finishing. The company offers additional services including material graining, grinding as well as powder coating to achieve the accuracy of their products.
The company works with a variety of materials, including Alumiconformsteel and carbon steel. Moreover, Prototek is ITAR registered and certified with ISO 9001 and AS9100 certifications that guarantee their fabrication conforms with the set industry standards.
They offer sheet metal fabrication services to suit various industries’ demands including aerospace, medical, and electronics industries.
Rank #07: SWF Industrial
Established Year: 1984
Country: United States
Address: Near York, PA, USA
Employee Size: 51-200
Core Business Capabilities:
- Sheet Metal Fabrication
- Laser Cutting
- Pipe Fabrication
- Robotic Plasma Cutting
- Plate Rolling
- Turning Rolls
Company Overview:
SWF was established in the year 1984 and emerged as the largest sheet metal fabrication companies in the world. The company employs 140 experienced employees whose expertise ranges from designing and engineering to project management and metal fabrication to meet its customers’ needs in its large, newly developed building.
The company specializes in precision work, focusing on carbon steel, aluminum, and other materials. A wide selection of metal forming services creates a solid and well-equipped company with design and drafting in-house. Their Pipe fabrication, laser cutting, robotic plasma cutting, leveling, and plate rolling services deliver high-quality products suitable for various industries.
SWF’s Metal Fabrication Capabilities:
- Pipe Fabrication (1/2 inch to 96 inches in size)
- Laser Cutting (up to 3/4 Carbon steel, 1/2 ‘ stainless steel )
- Robotic Plasma Cutting
- Plates that can be rolled up to 1” thick by a length of 10’ can be efficiently rolled and shaped with our plate rollers.
- Rolls Turning (up to 15 feet diameter)
Rank #08: RapidDirect
Established Year: 2009
Country: China
Address: Building A12, Haosi Industrial Park Nanpu Road
Xinqiao Street, Baoan District, Shenzhen, China, 518104
Employee Size: 201-500
Core Business Capabilities:
- Sheet Metal Fabrication
- CNC Punching
- Laser Cutting
- Bending
- Sheet Metal Welding (TIG, MIG/ FCAW, Spot Welding, Robotic Welding)
- Metal Stamping
Company Overview:
RapidDirect has only been in existence since 2009. It has quickly grown to become one of the dominant sheet metal fabrication companies. Based in Shenzhen, China the company applies AI technology in manufacturing settings to produce highly accurate sheet metal parts.
Having a reliable list of services offered, RapidDirect stands out as a manufacturer of bending, CNC punching, laser cutting, welding, and many others. The company is equipped with 40 state-of-the-art machines. Among these, 7 machines are Laser cutters which have 0.01mm accuracy and are capable of cutting 30mm thick plates.
RapidDirect deals in aerospace, automotive, and medical business, and offers prototypes as well as high production volumes solutions. In addition, it is ISO 9001:2015 certified to guarantee quality fabrication of all projects.
Key Services:
- Punching
- Arc welding (Tungsten Inert Gas, Metal Inert Gas, Spot, Robotic)
- Riveting
- Laser Cutting (Fiber and CO2)
- Bending
- Stamping
Rank #09: Kapco Metal Stamping
Established Year: 1972
Country: United States
Address: 1000 Badger Circle, Grafton, WI 53024, USA
Employee Size: 201-500
Core Business Capabilities
- Metal Stamping
- Laser Cutting (up to 1-inch)
- Welding
- Painting and Coating
- Pipe and Tube Fabrication
Company Overview:
Kapco Metal Stamping is the Midwest’s premier contract manufacturer of metal components. It is an Illinois-based company started in 1972 in the United States.
Kapco now operates eight plants covering 60,000 square feet and employs over 600 employees to provide top-quality sheet metal products.
At Kapco in-house, high-power lasers 4K, 6K, 10K, 15K, and CNC machines are used for fabrication. They have 17 brake presses ranging from 200 to 250 tons for semiconductor maintenance, along with 50 hydraulic and mechanical presses.
Kapco serves medical, defense as well as semiconductors sectors, high-stakes parts. The firm maintains a professional emphasis of strictly no compromise on quality. Kapco receives extra attention for the vertically integrated nature of its manufacturing and precision.
Rank #10: Xometry
Established Year: 2013
Country: United States
Address: 1300 K St NW, Washington, DC 20005, United States
Employee Size: 1k-5k
Core Business Capabilities:
- Waterjet Cutting
- Laser Cutting (CO2, Nd, Nd: YAG)
- Plasma Cutting
- Bending and Forming
- Welding
- Surface Finishing: Anodizing, Plating, and Powder Coating.
Company Overview:
Xometry is an innovative sheet metal fabrication company based in the USA. It holds a reputable position because of the integration of advanced technology. They focus on adhering to strict manufacturing specifications, particularly ISO 2768 for metal parts.
Xometry provides a broad range of services right from CNC machining and bending to welding and sheet metal cutting. The company also offers precision cutting services including CNC laser cutting, water jet cutting, and CNC plasma cutting.
In addition, xometry provides immediate turnaround times, achieving parts in 10 days or less. Their sheet metal work range has thicknesses from 1.0mm up to 40mm of aluminum, steel, and stainless steel while the cutting dimension for thicker sheets is up to 1500×6000mm.
Xometry also offers multiple tolerance options consistent with ISO 2768 and ISO 286, guaranteeing the quality of the finished products across industries.
Summary
In this article, we have presented the List of Top 10 Leading Sheet Metal Fabrication Companies based in China, the USA, and Europe. These companies are at the forefront of sheet metal fabrication providing various fabrication solutions to clients globally.
TECHNOLOGY
The Importance of Technology in Crafting Engaging, Randomized Game Experiences
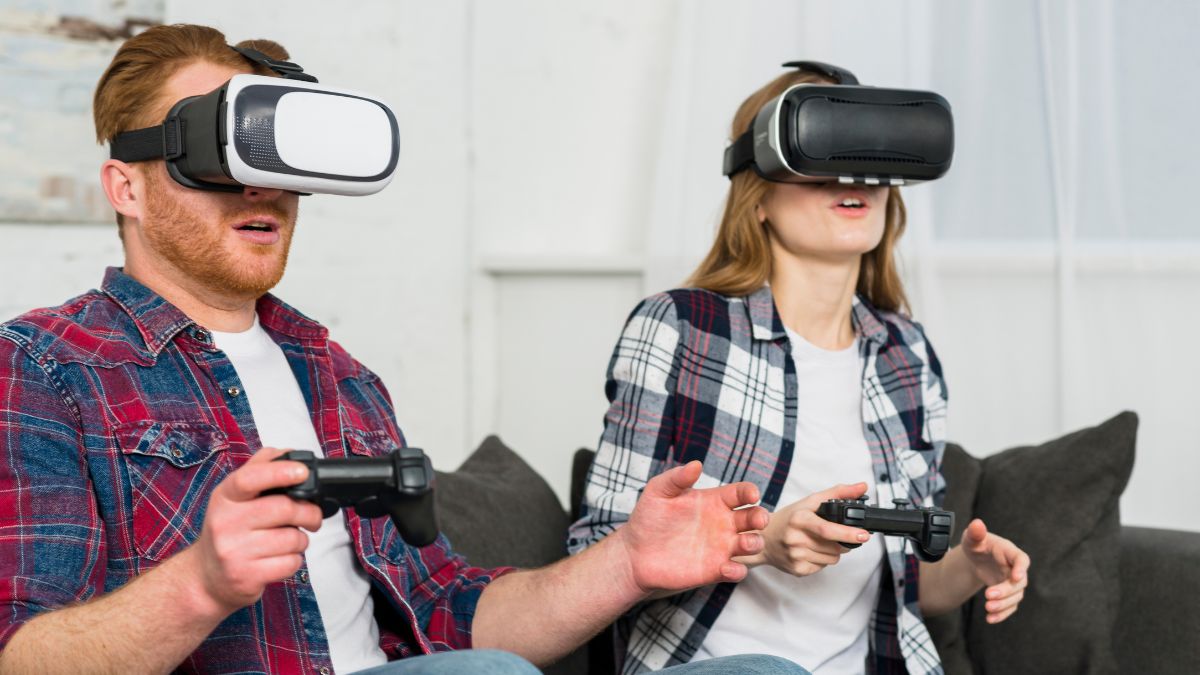
The demand for engaging experiences has never been higher, and developers must innovate constantly. From immersive graphics and artificial intelligence to randomized elements that keep players coming back for more, technology improves all aspects of game design.
Gamers now expect innovative gameplay that challenges their skills and delivers entertainment. Technology calls for creativity, technical expertise, and a deep understanding of players. The fusion of technology and gameplay mechanics transforms randomization into thrilling experiences that captivate audiences.
Improved Gameplay with Randomized Elements
Randomization is a powerful tool in modern game design: it introduces unpredictability and makes each gaming session unique and engaging. The evolving capabilities of technology allow developers to implement sophisticated algorithms that can generate diverse scenarios and outcomes. By integrating randomized elements, developers keep players on their toes and encourage replayable gameplay.
In certain games, character abilities, terrain, or mission objectives can be randomized. The use of a ludo dice roller introduces an element of chance, affecting strategies and outcomes in multiplayer games. Players appreciate the thrill of uncertain moments to improve their enjoyment. The introduction of random challenges or events can spur excitement, inviting players to adapt their strategies dynamically.
The Role of Artificial Intelligence in Game Randomization
Artificial Intelligence (AI) is revolutionizing how games are designed and played. AI-driven systems allow developers to create more intelligent and adaptive gameplay experiences. By using AI, designers can generate personalized experiences tailored to the player’s skills and preferences. Machine learning algorithms analyze players’ behaviors and adjust game elements accordingly.
AI can simulate random events, offering players opportunities and surprises. In open-world games, AI can control NPCs that react unpredictably. Continuous advancement in AI technologies enables developers to elevate the potential for randomization. AI enriches gameplay and promotes longevity in games through continuous engagement.
Big Data for Tailored Gaming Experiences
Big data analytics provides insight into player behavior and preferences, allowing developers to craft gaming experiences. By analyzing player interactions, developers can identify patterns that indicate what features captivate users most. This data-driven approach results in more engaging and customized experiences.
Random elements can be refined based on player feedback so that the content remains relevant and exciting. Developers can analyze which randomized elements succeed and which do not, fine-tuning the game design for optimal engagement. With big data, designers can implement effective A/B testing, experimenting with different randomization strategies to find the best fit. The alignment of gameplay mechanics with player preferences encourages improved satisfaction.
The Impact of Graphics and VR Technologies on Engagement
The quality of graphics can add to the player experience, making games more appealing and immersive. High-definition visuals create believable worlds so that players fully engage with the story and environment. Complementing those visuals, virtual reality (VR) technology has unlocked entirely new dimensions of engagement. With VR, players experience games from a new perspective, temporarily immersing themselves in the game world.
Randomization in VR games can lead to exciting outcomes; every session can feel unique. Players in a VR environment may encounter different scenarios or challenges each time, encouraging repeated gameplay. The combination of graphics and VR technologies guarantees that players are not just passive participants but active agents in the gaming experience. The potential for captivating randomization increases.
Keeping Players Engaged through Multi-Platform Experiences
Multi-platform experiences reach a broader audience. Players can transition between devices and maintain game continuity. By incorporating randomization in multi-platform games, developers keep players engaged regardless of where they play. Thanks to cloud gaming, professionals and casual gamers can enjoy the same experience in different environments. This flexibility allows for randomized elements to be experienced universally, increasing player satisfaction.
Technological advancements are harnessed across different devices, broadening the game’s reach. Gaming companies can create expanded communities where players share their experiences universally, discussing randomized elements and strategies. Innovations in cross-platform play create lasting connections among players..
The Future of Technology in Game Development
The potential for engaging in randomized experiences in gaming only expands. Upcoming innovations in artificial intelligence, big data, and graphics promise to create even more immersive platforms. Augmented reality (AR) may further improve interaction, allowing for more contextual randomness in how players engage with game environments.
Advancements in hardware capabilities will enable developers to implement more complex algorithms for randomized game design. Game developers must anticipate these trends and adapt to harness technology effectively while being mindful of player experience. As competition intensifies, those who leverage technology creatively will redefine the gaming industry. Through continued investment in innovative practices, the future of gaming looks promising for creating unique experiences that engage and excite.
Technology shapes the gaming landscape. Randomization promotes unique experiences; tools like AI and big data provide invaluable insights. As technology evolves, the potential for new and exciting forms of gameplay expands so that players remain engaged and entertained. The future promises even more creativity in the gaming industry.
- Cartoon1 year ago
Unlocking the Potential of Nekopoi.care: A Comprehensive Guide
- Game1 year ago
Exploring Aopickleballthietke.com: Your Ultimate Pickleball Destination
- BUSINESS1 year ago
What Companies Are In The Consumer Services Field
- BUSINESS1 year ago
Unraveling the Mystery of 405 Howard Street San Francisco charge on Credit Card
- HOME IMPROVEMENT1 year ago
Vtrahe vs. Other Platforms: Which One Reigns Supreme?
- TECHNOLOGY1 year ago
The Guide to Using Anon Vault for Secure Data Storage
- ENTERTAINMENT11 months ago
Understanding Bunkr Album: A Comprehensive Guide
- ENTERTAINMENT1 year ago
The Epic Return: Revenge of the Iron-Blooded Sword Hound